Reflow Soldering Definition
Reflow soldering involves applying solder paste to a printed circuit board (PCB), placing electronic components on the paste, and then controlling the temperature profile to melt the solder paste and form solder joints, thereby connecting the components to the PCB.
The working principle of reflow soldering is to heat the solder paste on the board’s pads, causing it to become liquid and connect the leads of surface mount components to the pads. This process is divided into several stages: first, preheating; then heating the solder paste to its melting temperature and holding it there for a period to ensure complete melting; and finally, rapid cooling to solidify the solder, creating a strong connection.
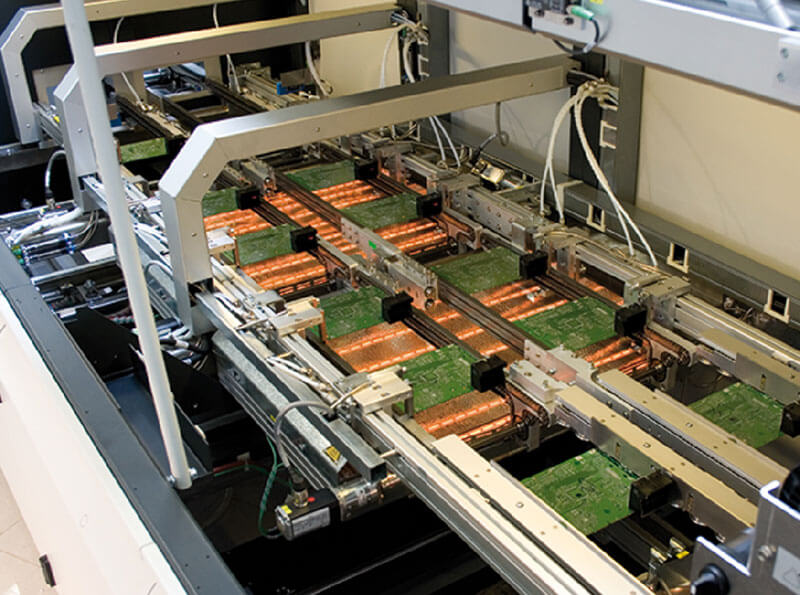
FAQs
Wave soldering and reflow soldering are two soldering techniques that are totally different from each other. In wave soldering, the components are soldered, with the help of wave crest, which is formed by a melted solder. Reflow soldering is soldering the components, with the help of reflow, which is formed by hot air.
Reflow Soldering for PCB Manufacturing
1.Solder Paste. Apply solder paste to the board that requires soldering.
2.Pick and Place. Apply the solder paste on the board and then place the components you require.
3.Preheat. Bring the board to the required temperature.
4.Thermal Soak.
5.Reflow.
6.Cooling.
*Source:https://www.candorind.com
The most common way of soldering electrical components on a circuit board is by using an oven. This process is known as reflow soldering. However, you can use a soldering iron and solder paste to achieve the same results.
*Source:https://www.conro.com
Reflow soldering is the standard process in the manufacturing of most electronic assemblies. Selective soldering allows us to protect delicate components and ensure that they are secure to the PCB, while also providing a reliable and consistent connection.
*Source:https://www.pgftech.com
Zero Defect
Quick-turn service
PCBA Manufacture
Learn how Keep Best can turn your designs into products.