Through-hole PCB Assembly
We will provide you with the solution that is best suited to your needs
Through-hole technology
THT is the abbreviation for through-hole technology. In contrast to fully automatic SMT assembly, in the THT process the wire ends of the components are mostly inserted manually into holes in the build board – hence the German name “through-hole assembly” – and then soldered “from below”. The THT assembly method is particularly suitable for large components involving heavy mechanical loads or high currents. In other words: the circuit boards have to meet stricter requirements. In PCB assembly practice, SMT and THT are often combined.
Application of THT welding process
Although SMT assembly has become increasingly important in recent years, THT assembly remains indispensable. THT assemblies create a strong connection between the component and the circuit board. This makes them ideal for larger components (such as transformers and semiconductors) that are exposed to high power, high voltage, and mechanical stress.
Since the components are actually inserted through the circuit board, they can withstand environmental stress more reliably. THT components are also easy to replace, making them ideal for prototypes and testing.
- Wave soldering system
- Selective soldering system
- Manual soldering
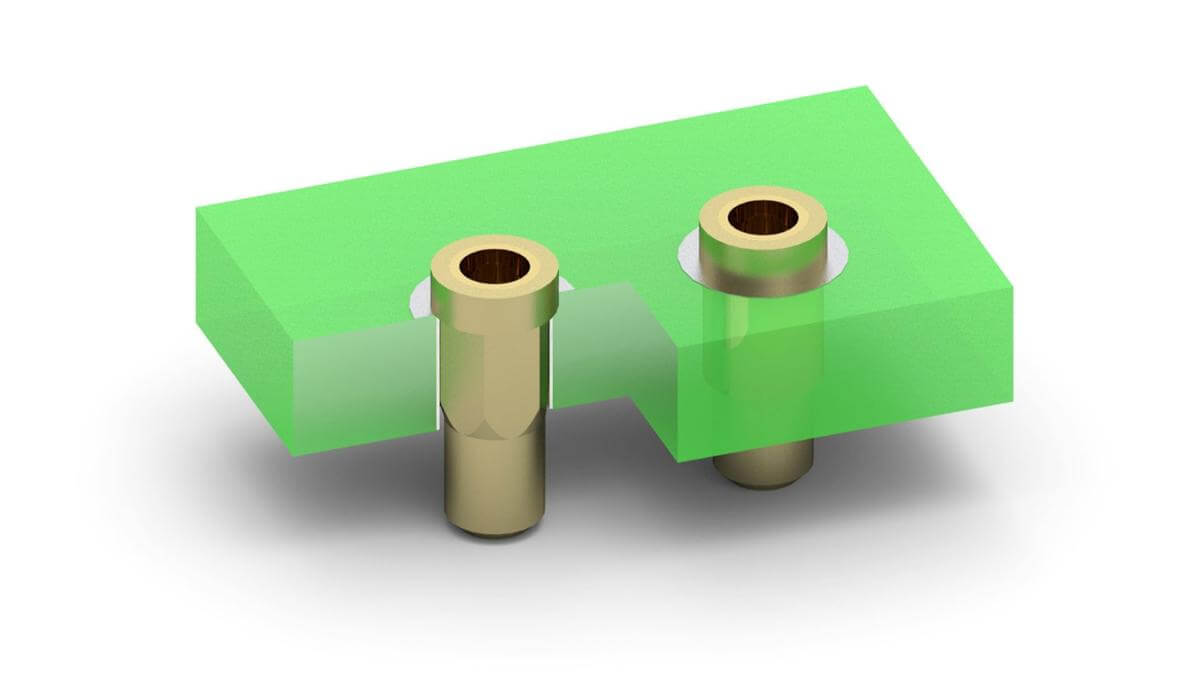
Wave Soldering System
The circuit boards pass through the wave soldering system in a special soldering frame, which triggers the corresponding soldering process via a transponder. The solder bubbles up from the underside of the circuit board. It wets the underside but only adheres to the pins and ensures permanent contact after cooling. With the wave soldering system, we can solder complete circuit boards in just a few seconds. Wave soldering is also very reliable. Combined with its speed, this property makes wave soldering ideal for large-scale PCB assembly. Wave soldering systems consume very low amounts of solder, as the solder can be reused.
We use ERSA wave soldering systems for soldering with leaded or lead-free solders.
Selective Soldering Systems
In a selective soldering system, solder is dispensed from a small nozzle. It automatically moves under the board and applies the solder joint at a defined point. The closer the components are to each other, the smaller the solder nozzle must be. For machine selective soldering, the distance between the SMT component and the THT solder joint should be at least 2.5 mm. Our ERSA selective soldering systems are equipped with a single or double solder pot for lead-free solder. Selective soldering is usually carried out in three steps:
- Applying flux. The flux improves the wetting of the pins to be soldered and removes any oxide layer that may have formed. The flux also reduces the interfacial tension.
- Preheating and PCB assembly. Preheating helps to optimize the soldering process and avoid thermal shock.
- The actual soldering is carried out using the solder nozzle. This is tailored to the specific requirements of the board.
Manual welding
In some cases, our employees also perform manual soldering. This is the case, for example, if the quantities are small. This saves us the initial costs of automation. We also manually solder temperature-sensitive components such as batteries or cables. In addition, manual soldering supports machine selective soldering if the components have been applied to the bottom side using SMD processes.
All our soldering processes are carried out using protective gas. We use nitrogen instead of oxygen, thus preventing unnecessary oxidation. The advantage: You get visually and technically perfect soldering results.
KEEP BEST PCBA's technical advantages
- Whether prototypes, small series or large series with THT assembly: We realize your ideas with precision manufacturing.
- High component mix? Of course, that’s no problem for us. We plan the assembly process efficiently.
- We test the technical feasibility of your order in advance.
- If you wish, we can optimize the settings for efficient production of your components. We are happy to work closely with your development department.
- We plan material logistics for the long term with international sourcing and efficient local warehousing.
We assemble a wide variety of THT components including resistors, capacitors, diodes, transistors, connectors, coils, transformers and more.
In SMT (Surface Mount Device) assembly, components are soldered directly on the surface of the circuit board, while in THT assembly, components are inserted through holes in the circuit board via wires and soldered. THT is often used for assemblies that require greater mechanical stability or larger designs.
Yes, we also provide PCB manufacturing. We can provide you with single-sided, double-sided, multi-layer, flexible and rigid-flex PCB.
Yes, we work with you from the beginning to refine your design for optimal manufacturability and to further improve reliability and quality.
Yes, we offer a comprehensive sourcing service and can provide all the components you need for your THT assembly.